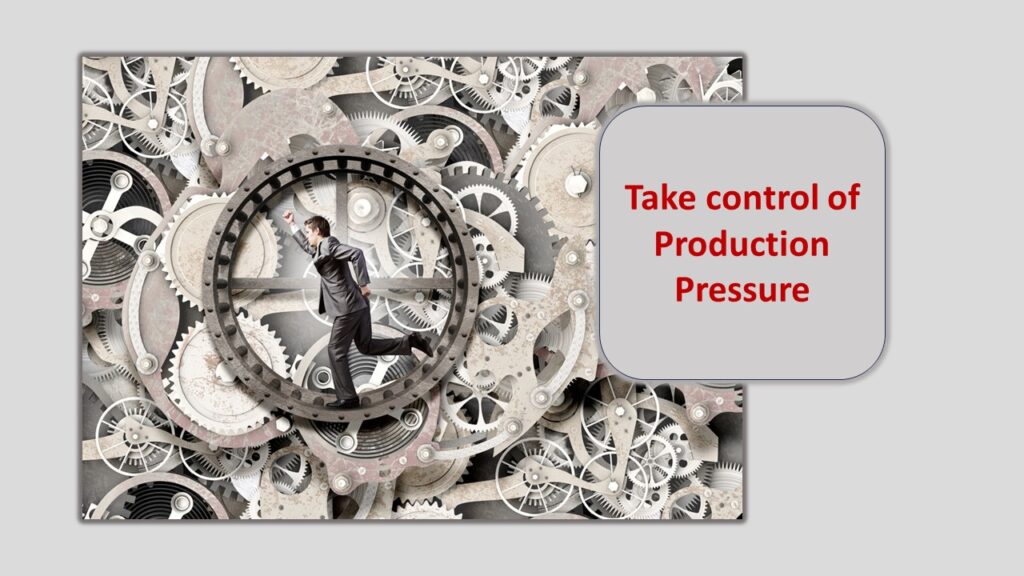
By Thomas Davis, DNAP, MAE, CRNA
In November of 1999, the Institute of Medicine shook America’s healthcare consumers when they released their report “To Err is Human.” The report noted that up to 98,000 patients were being harmed each year by medical errors. The healthcare community responded with an endless line of safety initiatives meant to protect the patient, however in the past 23 years, the safety numbers have not changed significantly. What is driving those numbers and what can we do to make the operating room a safer place for our patients?
Many factors contribute to medical errors and two common causes that are high on the list are production pressure and its byproduct, normalization of deviance. Understanding and controlling those two important contributing factors will position you to become a leader in patient safety.
What is production pressure?
Writing in the AANA Journal, authors Evans, Wilbanks and Boust define production pressure as “the emphasis on increasing efficiency, output, or continued productivity to increase monetary gain at the expense of patient safety.” Writing for the Agency for Healthcare Research and Quality, author Pascuale Carayon PhD reinforces the definition noting that production pressure involves both overt and covert pressures and incentives to place production, not safety, as the primary priority.
Definitions are nice but as CRNAs we know first-hand what production pressure looks like. Being called in early to get the extra case done before the posted schedule starts, being judged by how quickly the next patient gets into the room, staying long after fatigue has set in to do the add-on case. These expectations are rationalized by the benefit on the bottom line of the organization through an increase in case numbers. The unfortunate downside is that increased productivity is frequently attained by the risky practice of normalization of deviance.
What is normalization of deviance?
Normalization of deviance is the theory that minor deviations can be managed and tolerated. Writing for the Anesthesia Patient Safety Foundation, author Richard Prielipp notes “the normalization of deviance process breaks the culture of safety and applies equally to clinical anesthesia practice. Production pressure is frequently cited as a major driver of normalization of deviance and causes providers to work even when fatigued, create workarounds for safety systems, stretch the boundaries of hospital or departmental guidelines, and expedite patient care to the point of “cutting corners in the interest of staying on schedule.”
Production pressure, normalization of deviance and wrong site surgery.
When reviewing literature related to normalization of deviance, the crash of the space shuttle Challenger is a prime example of what can go wrong when decision makers bend the established policy and thinking that nothing bad will happen. In the operating room, wrong site surgery is equally devastating as the tragic explosion of the Challenger and leaves one to wonder how it could happen.
Wrong site surgery is an event that should never happen, however, the National Institute of Health reports that wrong site surgery occurs up to 40 times per week. This statistic exists despite the universal precautions of preoperative verification, marking of the operative site and the surgical time out. How does this happen? Production pressure encourages cutting corners and when nothing bad happens, more corners are cut until eventually a tragic event happens.
Be a high reliability organization.
Author Amanda Bonser notes that “high reliability” describes an organizational culture that strives to achieve error-free performance and safety in every procedure, every time, while operating in a complex, high-risk, or hazardous environment. Providing high reliability requires an element of frontline empowerment where healthcare providers can slow the process and ensure that policies and procedures are followed as intended in every surgical case. In high reliability environments, there is a reluctance to simplify or cut corners and exploring the root cause and understanding a failure is more important than bragging about the things that go well. At the heart of a high reliability mentality is the refusal to be pushed to compromise any part of the surgical process. Likewise, it is equally important not to pressure others to make compromises.
Develop a traffic circle mentality.
For decades, traffic engineers have sought to design intersections that eliminate the possibility of death or major injury. Knowing that the highest risk scenario is a left turn on a high-speed road, engineers are installing traffic circles at high-risk intersections. When approaching a traffic circle, drivers are forced to slow the pace, assess the danger of other cars in the circle, make eye contact and coordinate with other drivers and then safely navigate through the intersection. Even though fender benders may occur, it is almost impossible to have a fatal crash in a traffic circle.
Developing a “traffic circle” mentality with each surgical patient requires that providers slow the pace, assess potential risks to the patient, coordinate with others and finally, successfully perform the surgical procedure. In such a scenario, safety is more important than speed, the needs of others are recognized, and patient safety is the top priority. Using a traffic circle mentality in the operating room with an emphasis on slowing the pace while communicating and coordinating with everyone on the team eliminates the need to cut corners and makes it almost impossible for events such as wrong site surgery to occur.
Every time you allow yourself to be pushed or you push another person on the team to value productivity over safety you are inviting a sentinel event in your operating room. Develop a traffic circle mentality and transform your workplace into a high reliability organization.
Tom is an experienced leader, educator, author, and requested speaker. Click here for a video introduction to Tom’s talk topics.